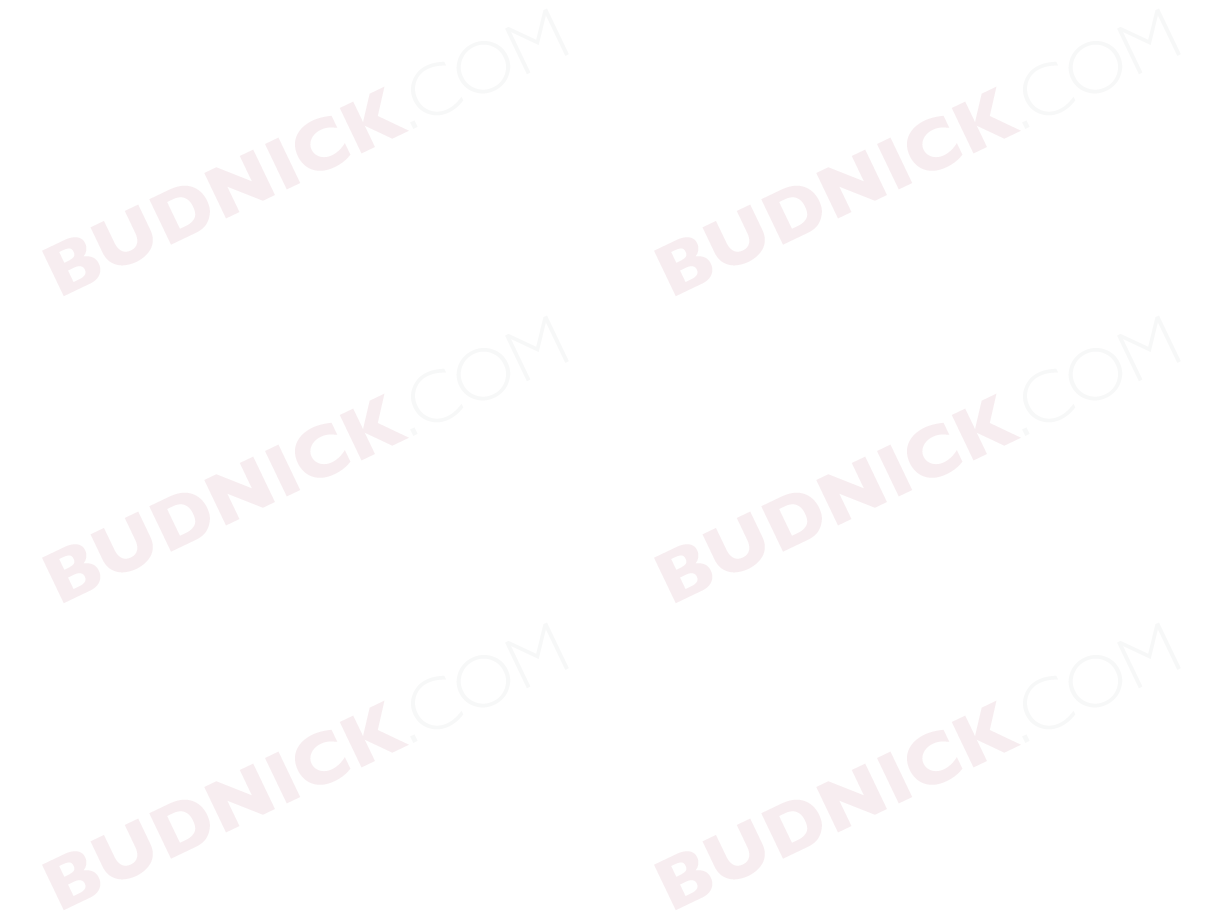
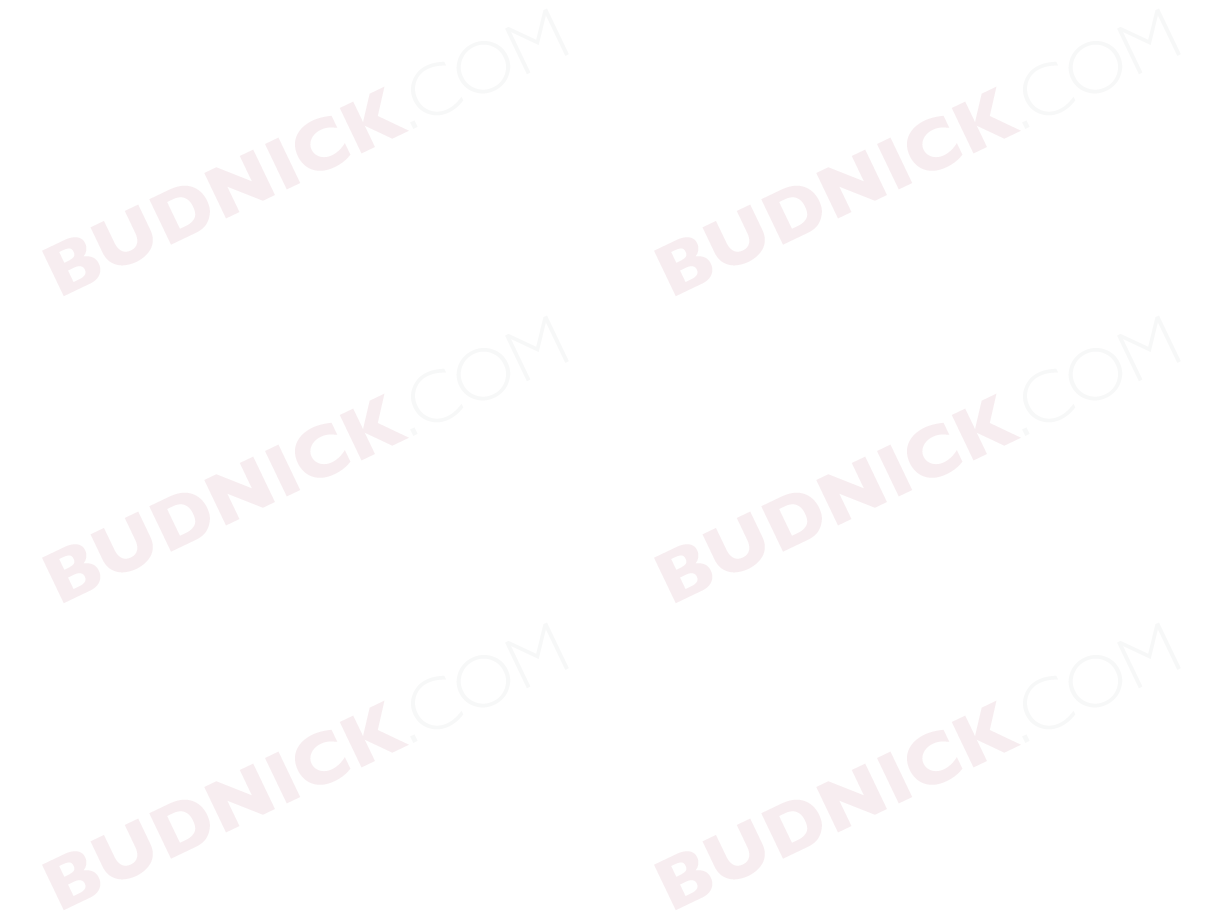
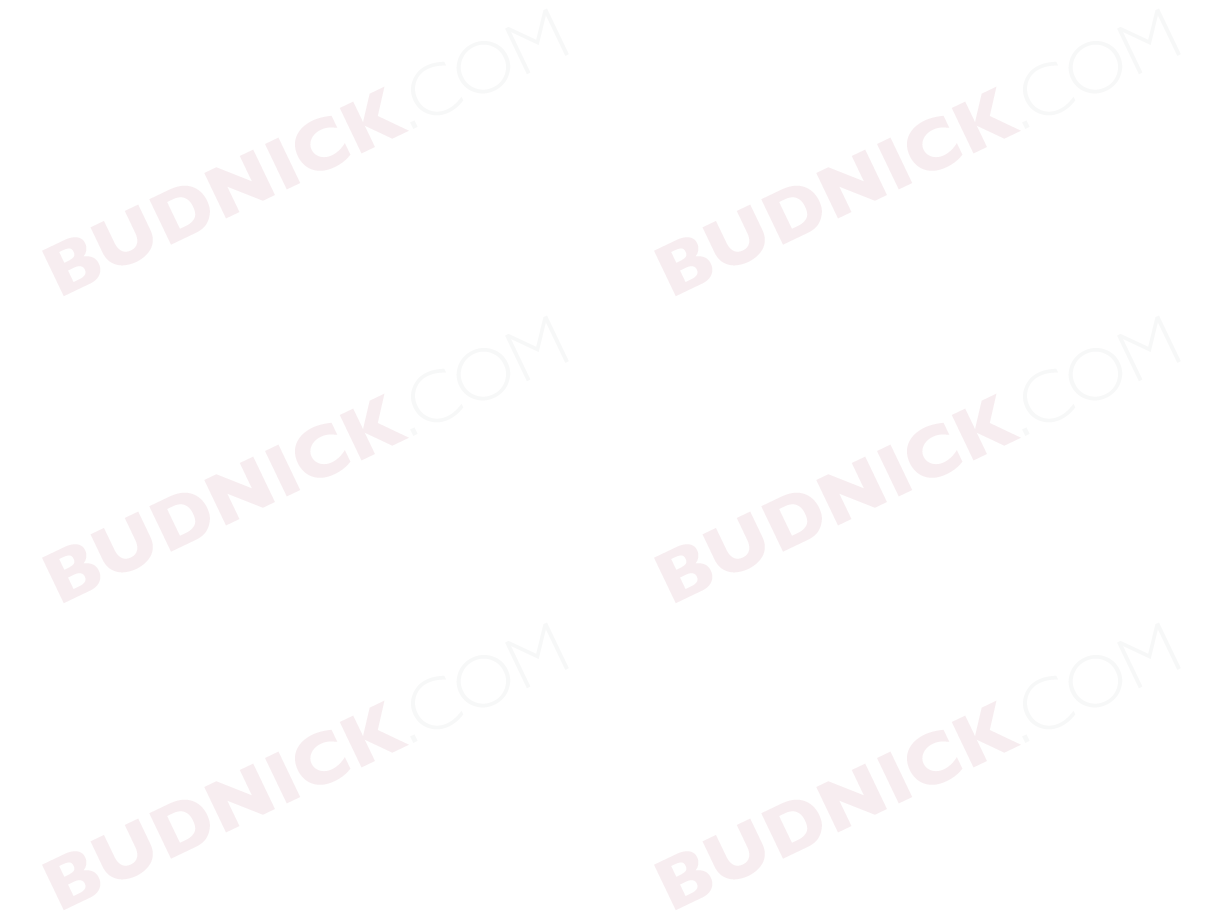
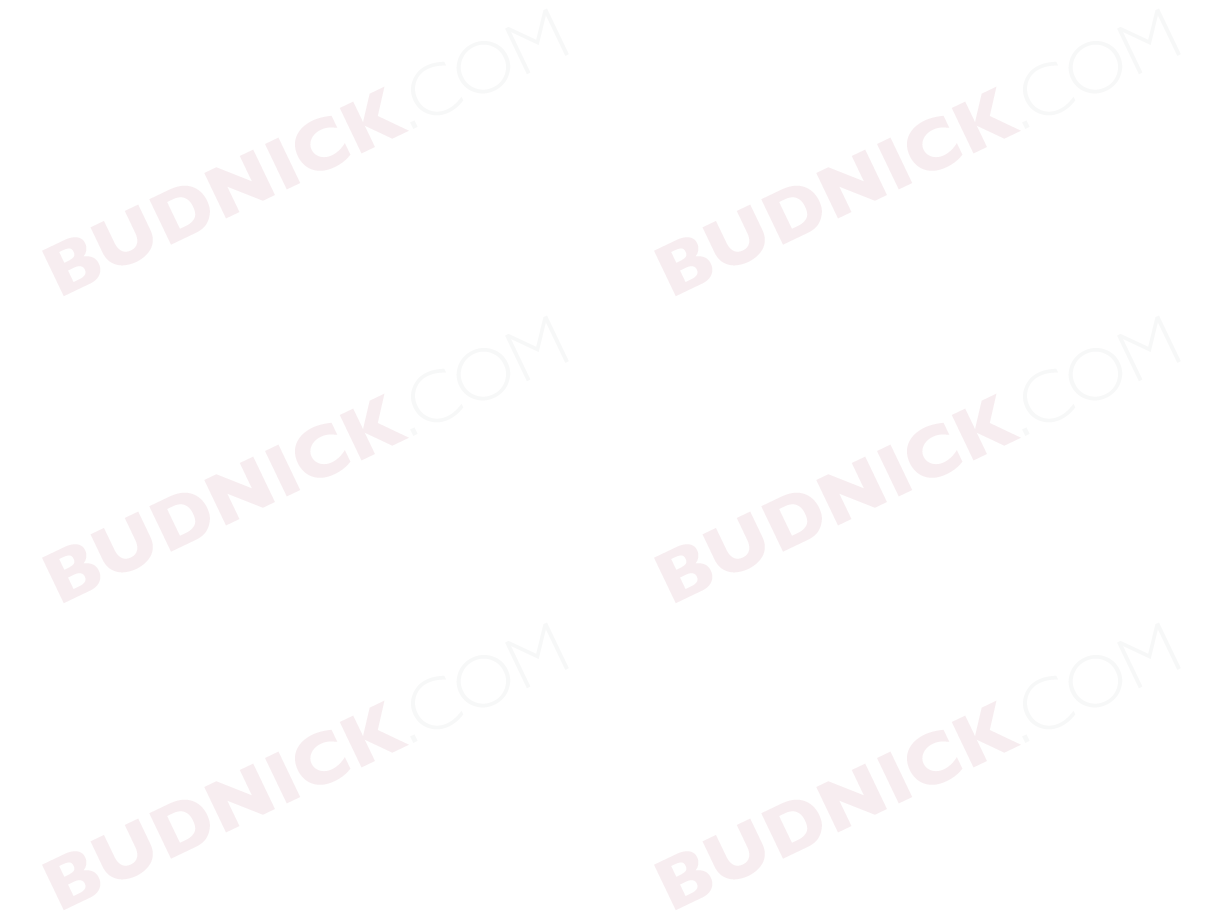
Tape101
One of the biggest missteps you can make in your adhesive selection process is assuming that all tapes are the same - which is why we're here to help you understand the differences.
Get the eBook
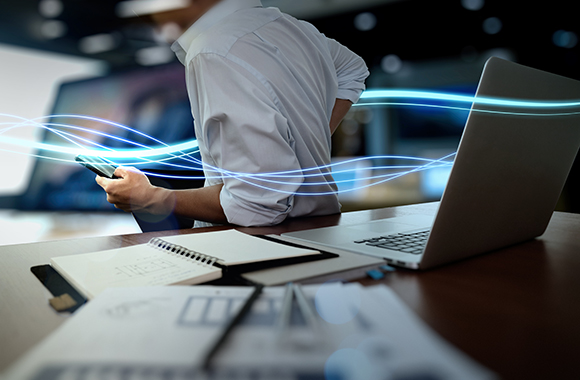
One of the biggest missteps you can make in your adhesive selection process is assuming that all tapes are the same. So much goes into whether an adhesive will work for your specific application, and you should consider each factor when picking out an ideal product. It's important to match the properties of your adhesive to the needs of what you're bonding.
At Budnick.com we've always made it our primary goal to educate our customers as best we can, and our Tape101 eBook and learning center is the next step in that process. We've outlined the basic steps to follow and questions to ask throughout the process of identifying an adhesive so you can approach each project with the knowledge you need to make the best decisions. Feel free to browse through the basics of tapes, or for a more in-depth overview, download our free eBook here!
Case Studies
Budnick has decades of experience developing application, product, and process solutions - read about some of our favorite solutions below!
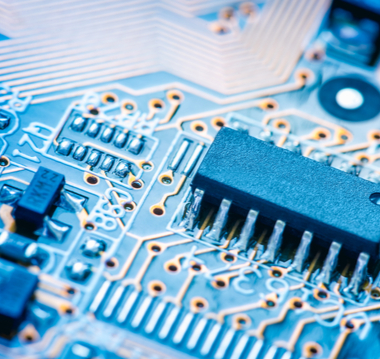
Case Study Reposition Thermal Interface
Finding a repositionable tape that bonds to silicone without interfering with thermal conductivity put Budnick’s tape experts to the test.
- Typically, silicone only bonds to silicone, but silicone tapes affected thermal conductivity
- Sufficient amount of testing took place before finding an acrylic transfer
- The acrylic adhesive did not prevent the heat transferring through the interface
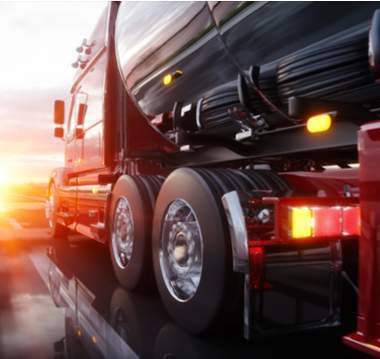
Case Study Mounting a Fuel Tank Emblem
A fuel tank manufacturer was spending excessive time hand cutting tape to the dimensions of their logo, only to see it fail to bond to the tank.
- Customer was using a film tape that was not a long-term emblem mounting solution
- Hand-cutting the tape was no longer a feasible option for the customer either
- Customer needed a tape that could withstand environmental elements

Security Panel Cover Attachment & Protection
Budnick's die-cutting capabilities and expertise with extended liners helped create user-friendly solutions for a major electronic automation and controls manufacturer.
- High bond 3M™ VHB™ Tape was die cut to the customer's exact specifications
- Added a 12 point liner that is stiff enough for easy release & and a finger-lift tab to simplify product assembly
- Designed packaging that would prevent shipping damage & also act as a dispenser unit for the parts