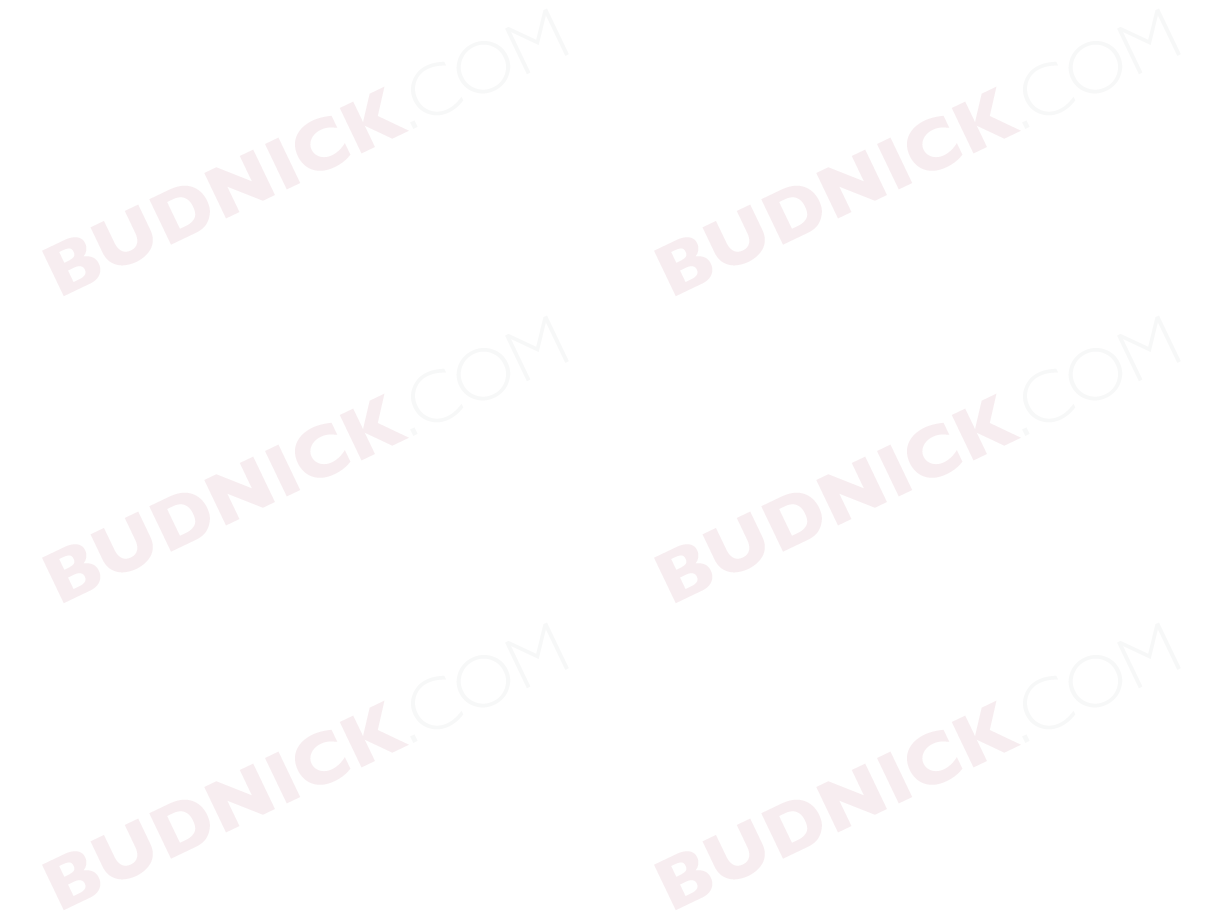
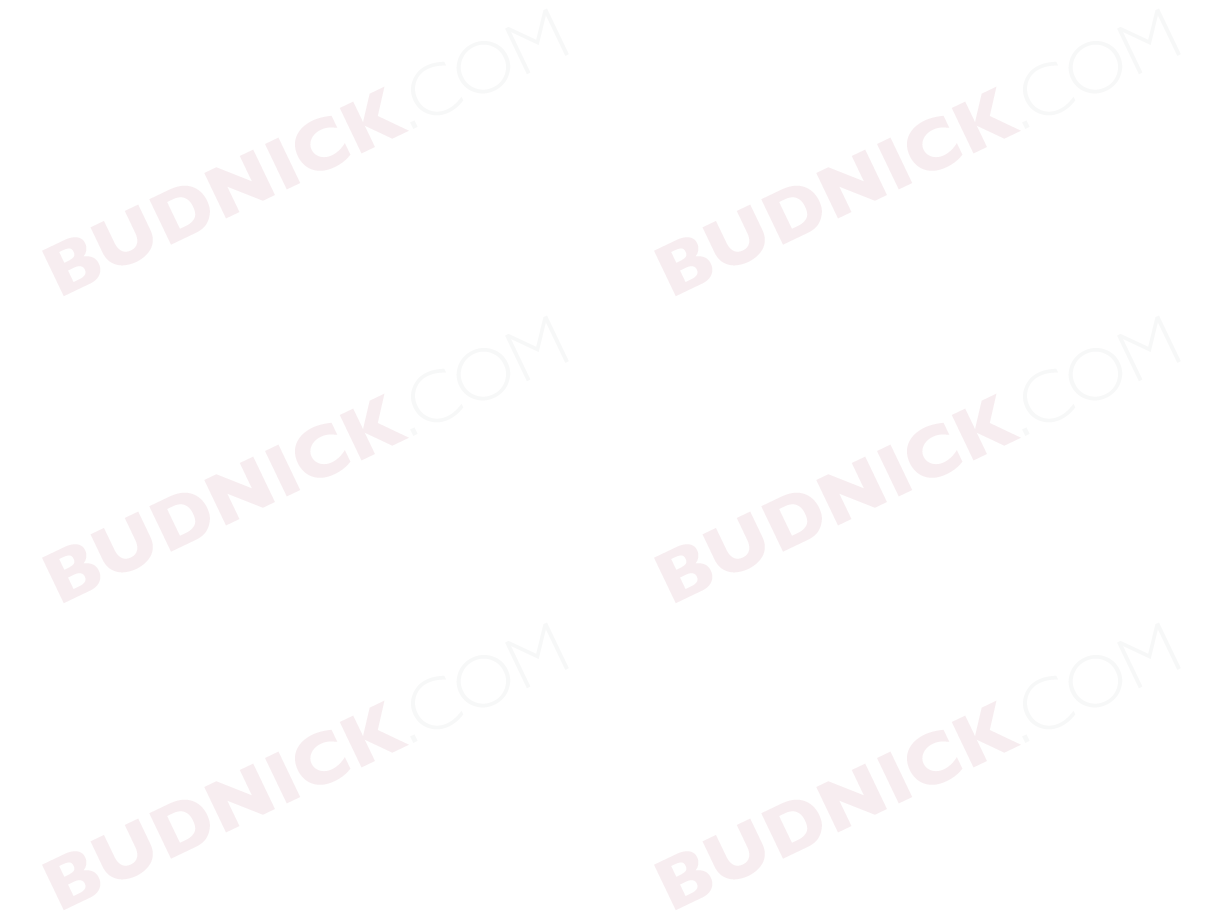
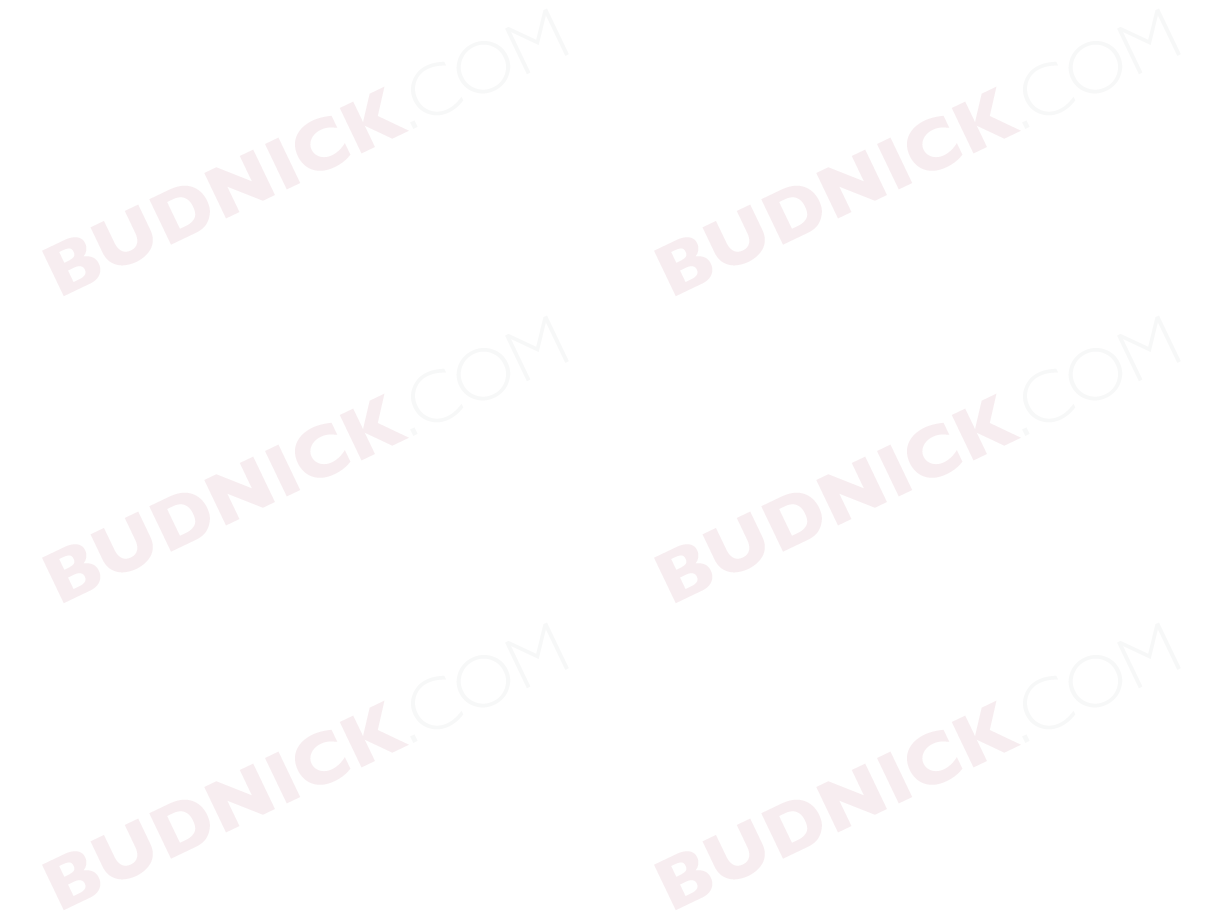
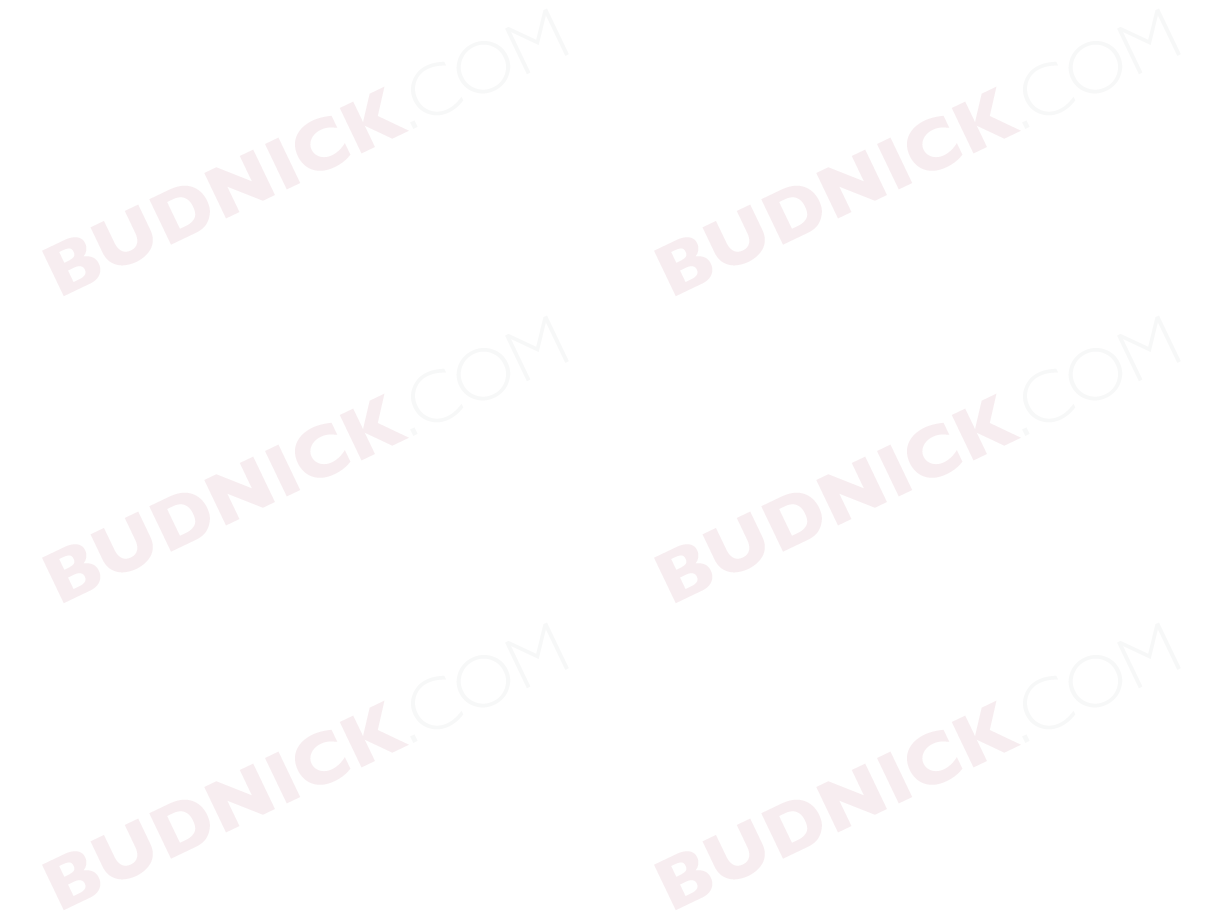
Die Cutting
Budnick die cuts adhesive tapes, foams, and other and flexible materials to a variety of custom shapes and sizes that can be provided on a sheet or on a roll
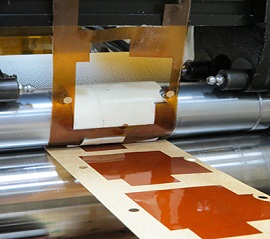
Rotary Die Cutting
Using precision engraved steel cylinders, we can quickly and easily die-, cavity-, kiss-, or butt-cut a wide variety of roll goods - both adhesive and non-adhesives tapes, foams, foils, plastics, and films up to 1/8" thick.
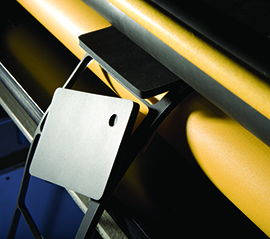
Flatbed Die Cutting
Flatbed die-cutting helps save money on tooling and accommodates thicker and softer material than most rotary methods allow. This process is ideal for shorter but still intricate production runs.
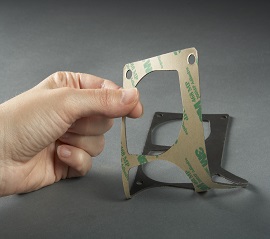
Specialized Capabilities
Advanced equipment allows us to minimize scrap and maximize runtimes and production efficiency - from longer length rolls and finger lift edges, to reduced scrap by spacing parts without a matrix.
What We Offer
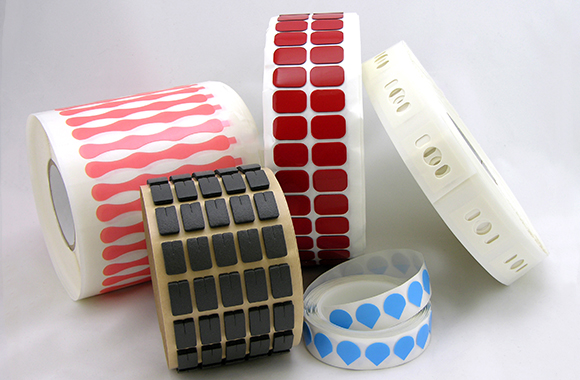
We have the versatility to die cut almost any material with a multitude of different processes and hit customer specs every time. Each machine and operator have different qualities that line up with individual customer needs and our years of knowledge makes Budnick the best in the industry. Our rotary presses allow us to provide both roll and sheeted parts while holding the tightest of tolerances. The flatbed department can work with tricky materials and still provide the edge quality and product consistency of a tooled part. Whether you’re looking for a doubled coated die cut adhesive in roll form for long production runs or a less dense individual foam part with tight tolerances we’ll find the right process and provide the right part every time.
Budnick Die Cuts: Tape | Pressure Sensitive Materials | Silicone Rubber | Fabric | Label Stock | Plastic Liner | Plastic | Gasket Materials | UHMW | Foil | Non-Woven | Foam | Silicone Foam | Abrasive | Specialty Materials | Rubber & More
Case Studies
Budnick has developed a series of proprietary die-cutting processes that lead to cleaner, more accurate cuts. Read on to learn how else we've improved our customers' processes!
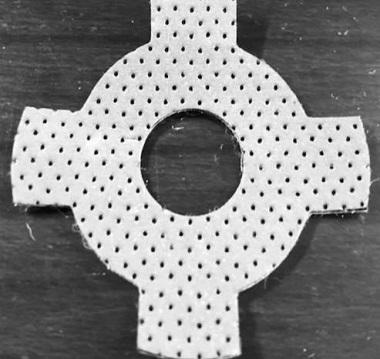
Conductive Die Cut Gasket for Electrical Grounding
A major appliance OEM needed an electrical grounding solution due to quality issues with wiring/lighting.
- Worked with 3M™ to provide products for testing
- Provided a die-cut gasket with electrically conductive properties
- Quick and easy to apply
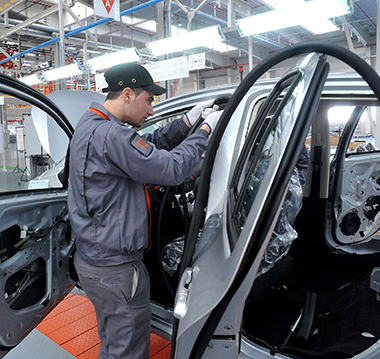
Case Study Converting Experts
An automotive supplier could only purchase rolled product, but the application called for short pieces
- Sheets containing four individual pieces met the customer's need
- A custom die was made to cut parts to length with a minimum amount of bevel on the product
- The material maintained its cord, and the presentation saved production time
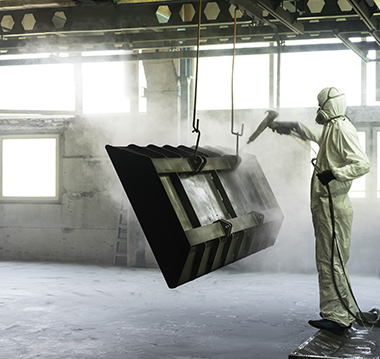
Case Study Enhanced Production
Lacking in production efficiency and healthy hands, this aerospace came to Budnick in search of solutions for a complex masking application.
- Workers were cutting tape by hand and often cutting themselves
- Tape was being cut for various sizes of metal parts to mask during shot peening
- After working with Budnick, the customer was able to double production